Comprehensive Guide: What is Porosity in Welding and Exactly How to avoid It
Porosity in Welding: Identifying Common Issues and Implementing Best Practices for Avoidance
Porosity in welding is a pervasive problem that typically goes unnoticed until it creates substantial problems with the integrity of welds. This common issue can jeopardize the strength and toughness of bonded frameworks, positioning safety threats and leading to costly rework. By understanding the source of porosity and implementing reliable avoidance methods, welders can substantially improve the top quality and dependability of their welds. In this conversation, we will certainly explore the vital elements adding to porosity development, examine its harmful effects on weld performance, and review the ideal methods that can be embraced to minimize porosity incident in welding processes.
Common Reasons For Porosity
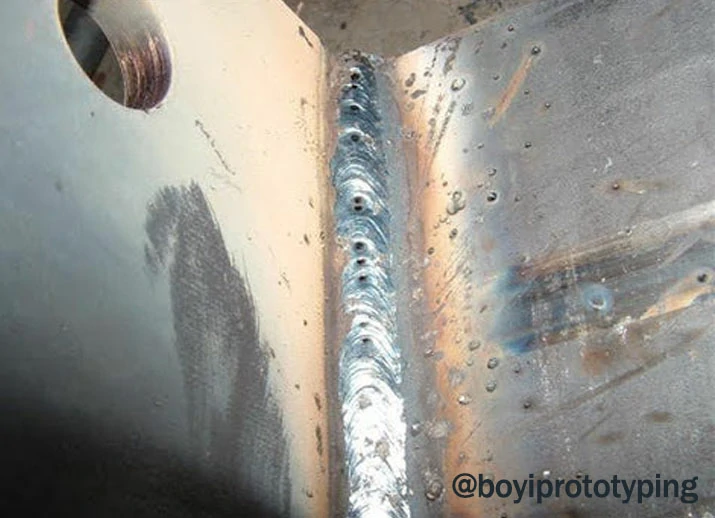
Another regular culprit behind porosity is the existence of pollutants externally of the base steel, such as oil, grease, or rust. When these pollutants are not effectively eliminated before welding, they can vaporize and become trapped in the weld, creating problems. In addition, using dirty or wet filler products can present impurities into the weld, adding to porosity problems. To alleviate these usual reasons for porosity, thorough cleansing of base steels, appropriate protecting gas selection, and adherence to optimal welding parameters are important practices in attaining high-grade, porosity-free welds.
Impact of Porosity on Weld Top Quality

The visibility of porosity in welding can considerably endanger the structural integrity and mechanical properties of welded joints. Porosity produces gaps within the weld metal, deteriorating its total strength and load-bearing capacity.
Welds with high porosity levels tend to exhibit reduced influence toughness and minimized capability to deform plastically before fracturing. Porosity can impede the weld's capacity to properly transfer forces, leading to premature weld failure and prospective safety and security risks in vital structures.
Best Practices for Porosity Prevention
To boost the architectural integrity and high quality Get More Info of bonded joints, what details measures can be carried out to reduce the event of porosity during the welding process? Utilizing the proper welding strategy for the specific material being welded, such as changing the over at this website welding angle and weapon placement, can better prevent porosity. Regular evaluation of welds and immediate remediation of any type of problems determined throughout the welding procedure are crucial techniques to prevent porosity and produce top quality welds.
Significance of Appropriate Welding Methods
Carrying out proper welding techniques is critical in guaranteeing the structural stability and quality of welded joints, building on the foundation of reliable porosity avoidance actions. Welding strategies straight affect the total strength and resilience of the welded framework. One vital element of appropriate welding techniques is maintaining the proper warmth input. Extreme warm can lead to increased porosity as a result of the entrapment of gases in the weld pool. On the other hand, inadequate heat might lead to incomplete blend, producing prospective powerlessness in the joint. In addition, utilizing the suitable welding parameters, such as voltage, existing, and travel speed, is important for achieving audio welds with very little porosity.
Furthermore, the choice of welding process, whether it be MIG, TIG, or stick welding, must straighten with the certain needs of the project to guarantee ideal outcomes. Proper cleansing and prep work of the base metal, in addition to selecting the right filler material, are additionally important components of efficient welding techniques. By adhering to these best practices, welders can minimize the threat of porosity development and create top notch, structurally sound welds.
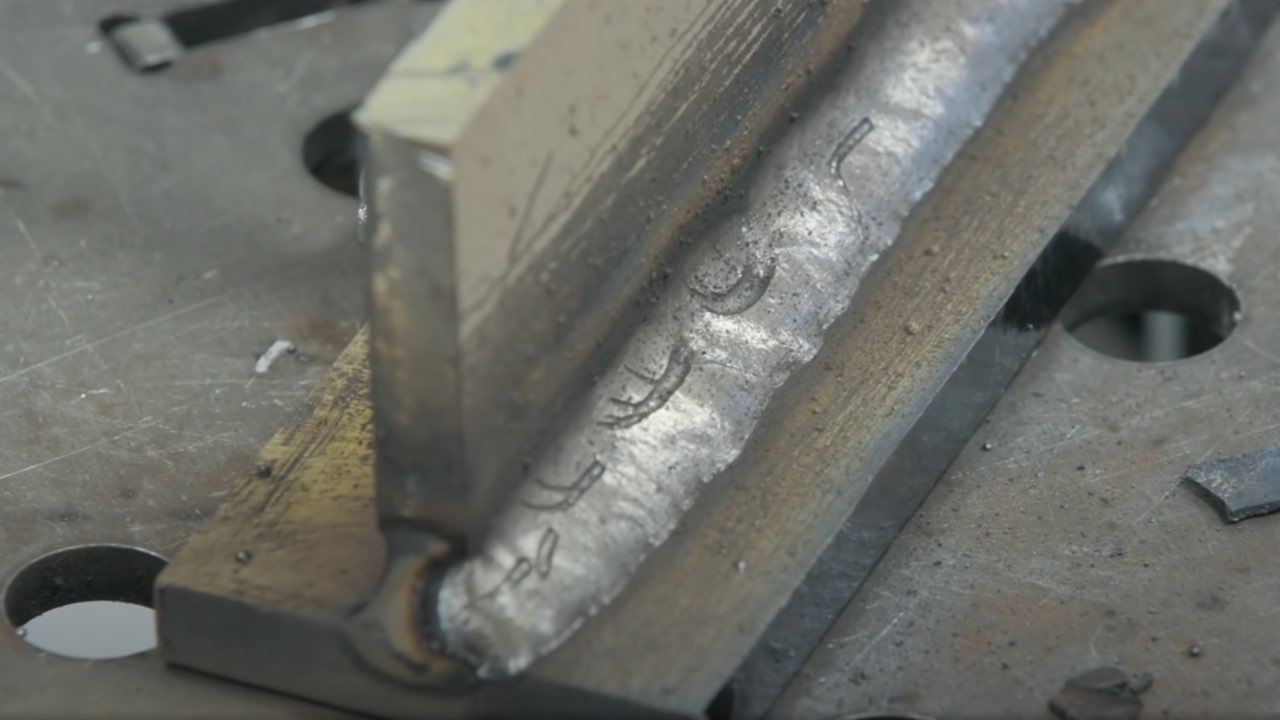
Examining and Top Quality Control Measures
Quality control measures play a vital role in verifying the stability and dependability of welded joints. Testing procedures are important to find and stop porosity in welding, making sure the stamina and resilience of the final item. Non-destructive testing methods such as ultrasonic screening, radiographic screening, and visual inspection are commonly employed to recognize prospective problems like porosity. These strategies enable the evaluation of weld high quality without jeopardizing the honesty of the joint. What is Porosity.
Post-weld examinations, on the other hand, assess the final weld for any type of issues, including porosity, and verify that it fulfills specified requirements. Implementing from this source a detailed quality control plan that consists of thorough testing treatments and inspections is critical to lowering porosity problems and making certain the overall high quality of welded joints.
Verdict
To conclude, porosity in welding can be a common problem that influences the top quality of welds. By identifying the common causes of porosity and carrying out ideal techniques for prevention, such as proper welding techniques and testing procedures, welders can make certain premium quality and dependable welds. It is vital to focus on avoidance approaches to decrease the event of porosity and keep the honesty of bonded frameworks.